Plastic extrusion for intricate profiles and custom designs
Discovering the Different Methods and Technologies Behind Plastic Extrusion
The world of plastic extrusion is a blend of precision, technology, and innovation, crucial to various industries worldwide - plastic extrusion. Advanced machinery, electronic controls, and an array of materials merge in this complicated procedure, creating high-quality, sturdy products. As the industry evolves, a change towards lasting products and intelligent equipment appears. The adhering to conversation will certainly shed light on these methods and technologies, while also hinting at the amazing future potential customers of this essential production process.
Comprehending the Fundamentals of Plastic Extrusion
The process of plastic extrusion, typically hailed as a keystone in the world of manufacturing, develops the bedrock of this discussion. In significance, plastic extrusion is a high-volume production process in which raw plastic product is thawed and created into a continuous profile. The procedure starts with feeding plastic materials, usually in the form of pellets, right into a heated barrel.
The Function of Different Materials in Plastic Extrusion
While plastic extrusion is a frequently utilized method in manufacturing, the products made use of in this procedure significantly influence its last outcome. Different kinds of plastics, such as pvc, polyethylene, and abdominal muscle, each lend special residential properties to the end product. Suppliers need to very carefully think about the properties of the product to enhance the extrusion process.
Techniques Used in the Plastic Extrusion Refine
The plastic extrusion process involves numerous techniques that are crucial to its operation and effectiveness (plastic extrusion). The discussion will certainly begin with a streamlined description of the fundamentals of plastic extrusion. This will be followed by a breakdown of the procedure thoroughly and an expedition of methods to enhance the performance of the extrusion method

Understanding Plastic Extrusion Fundamentals
In the realm of production, plastic extrusion stands as a basic process, necessary in the manufacturing of a plethora of daily products. At its core, plastic extrusion involves transforming raw plastic product right into a constant profiled form. This is achieved by melting the plastic, usually in the type of pellets or granules, and compeling it through a designed die. The resulting product is a lengthy plastic piece, such as a cable, panel, or pipe covering, that retains the shape of the die. This cost-efficient technique is very versatile, able to produce complex shapes and fit a wide array of plastic materials. Fundamental understanding of these basics permits additional expedition of the more elaborate aspects of plastic extrusion.
Detailed Extrusion Refine Breakdown
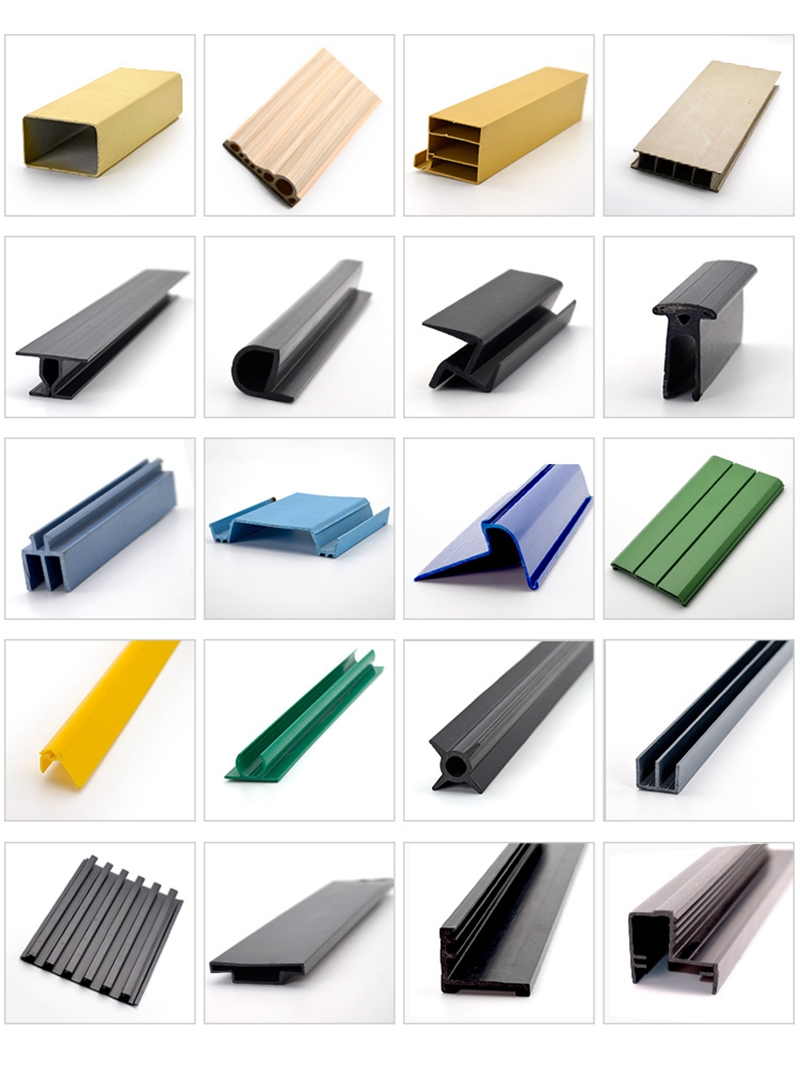
Improving Extrusion Strategy Efficiency
Efficiency gains in the plastic extrusion process can considerably influence both the top quality of the final item and the general productivity of the operation. Constant optimization of the extrusion strategy is important to preserving an affordable edge. Methods that improve performance usually involve precise control of temperature and pressure throughout the process. Modern technologies, such as electronic systems and sensors, have contributed in achieving this control. Additionally, using premium resources can lower waste and boost outcome top quality. Regular maintenance of extrusion equipment can likewise minimize downtimes, thus raising efficiency. Ultimately, taking on lean manufacturing principles can assist get rid of unnecessary steps in the process, promoting effectiveness gains.
Just How Modern technology Is Transforming the Face of Plastic Extrusion
The introduction of brand-new modern technology has dramatically changed the landscape of plastic extrusion. It has caused the growth of sophisticated extrusion machinery, which has improved the efficiency and quality of the plastic extrusion procedure. In addition, advancements in the extrusion procedure have likewise been driven by technological advancements, providing enhanced capabilities and flexibility.
Advanced Extrusion Equipment
Changing the world of plastic extrusion, progressed equipment imbued with cutting-edge innovation is ushering in a new age of performance and precision. These equipments, outfitted with ingenious features like automatic temperature control systems, ensure ideal problems for plastic handling, consequently lessening waste and improving item top quality. While these innovations are currently remarkable, the continuous development of innovation guarantees also greater leaps forward in the field of plastic extrusion equipment.
Innovations in Extrusion Processes
Taking advantage of the power of contemporary technology, plastic extrusion processes are undergoing a transformative metamorphosis. Technologies such as electronic mathematical control (CNC) systems now permit even more accuracy and consistency in the manufacturing of extruded plastic. Automation even more enhances performance, reducing human error and labor prices. The integration of expert system (AI) and artificial intelligence (ML) formulas is reinventing quality control, anticipating variances, and boosting the overall performance of extrusion processes. With the introduction of 3D printing, the plastic extrusion landscape is also expanding into brand-new realms of possibility. These technological innovations are not only boosting the quality of extruded plastic items but also thrusting the industry in the direction of an extra lasting, reliable, and ingenious future.
Real-World Applications of Plastic Extrusion
Plastic extrusion, a reliable and flexible procedure, finds use in plenty of real-world applications. It's mainly utilized in the manufacturing sector, where it's utilized to produce a myriad of items such as pipes, tubes, home window frames, weather removing, and secure fencing. The automotive industry also uses this innovation to produce parts like trim and plastic sheet. The medical area relies on extrusion for the construction of catheters, IV tubes, and various other medical devices. Even in food production, extrusion plays a duty in developing items like pasta or cereal. The stamina and flexibility of plastic extrusion, combined with its cost-effectiveness, make it a crucial procedure throughout different markets, highlighting its widespread functional applications.
The Future of Plastic Extrusion: Trends and forecasts
As we look to the perspective, it comes to be clear that plastic extrusion is positioned for considerable innovations and improvement. Environment-friendly choices Find Out More to standard plastic, such as bioplastics, are likewise anticipated to gain grip. These fads suggest Get More Info a dynamic, developing future for plastic extrusion, driven by technical technology and a commitment to sustainability.

Final thought
In verdict, plastic extrusion is a complicated procedure that uses sophisticated technology and differed materials to create varied items. Technological advancements, such as electronic controls, enhance the manufacturing procedure and make certain constant outcomes. In addition, the sector's focus on sustainability and smart machinery suggests an encouraging future. As plastic production continues to progress, it remains a crucial part of many sectors worldwide.
In essence, plastic extrusion is a high-volume production procedure in which raw plastic product is thawed and developed into a constant profile.While plastic extrusion is a typically utilized method in production, the products used in this procedure considerably affect its last output. At its core, plastic extrusion entails changing raw plastic product into a continuous profiled shape. It has actually led to the development of innovative extrusion machinery, which has actually improved the effectiveness and top quality of the plastic extrusion procedure.In conclusion, plastic extrusion is an intricate process that uses advanced browse this site innovation and differed products to develop diverse products.